Direct Write Printed Electronics on Complex 3D Surfaces
By Marcelino Essien
Direct-Write Printing is an emerging technology that enables the deposition of electrical circuits on various 3D structures. Aerosol Jet printing is a type of Direct-Write Printing that focuses and deposits aerosolized ink droplets in an ambient atmosphere, without the use of masks. Applications enabled by Aerosol Jetting range from metallization of 3D printed objects to printing of embedded electronic circuits in plastic parts.
Direct-write printing of various electronic components on 3D surfaces facilitates light-weighting, improves performance in extreme environments, and optimizes device footprints.
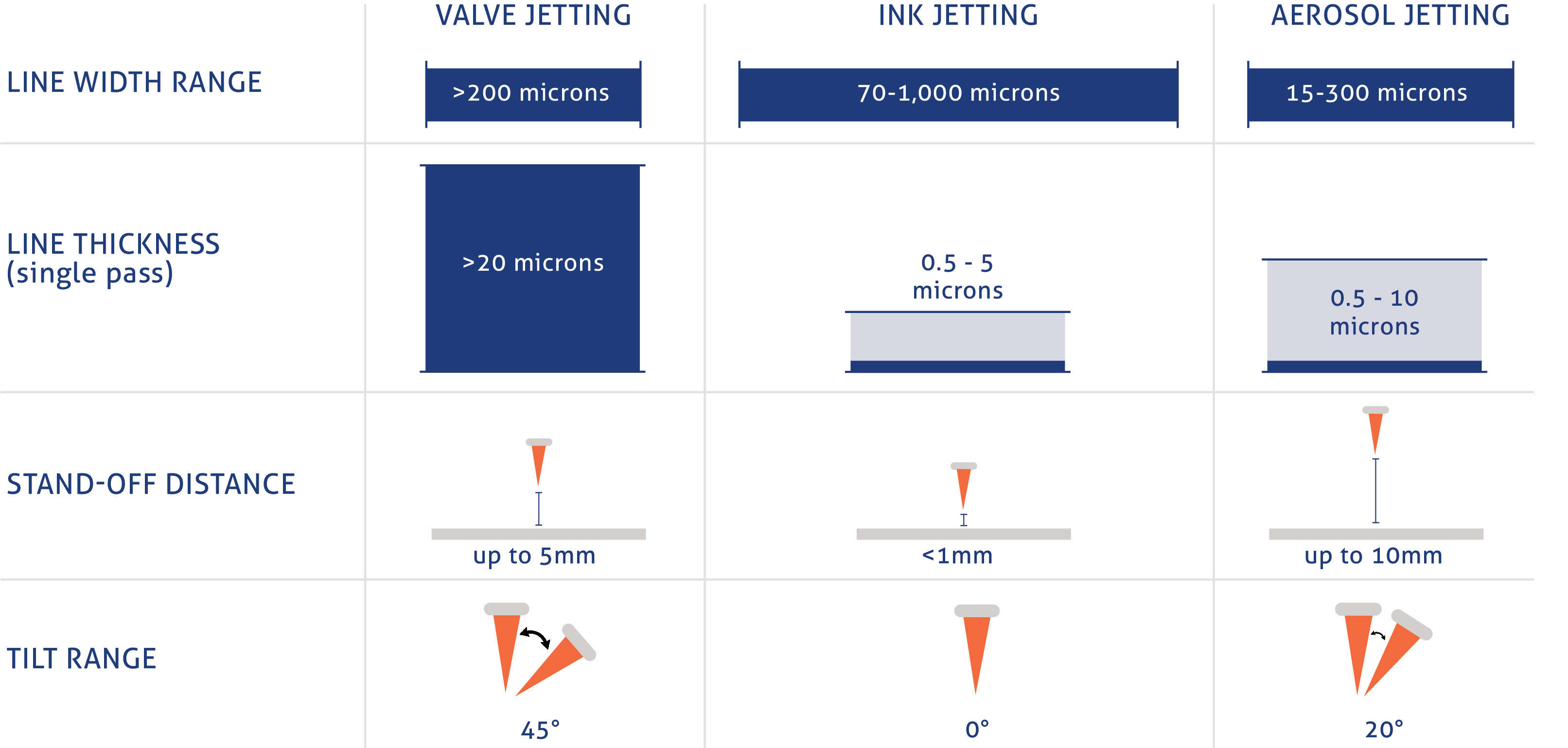
Exciting advances in Direct-Write printing of electronic components on complex 3D substrates are realized with Aerosol Jetting. Complex 3D surfaces require large, variable stand- off distances and a significant tilt range between the printhead and the substrate for Direct-Write printing of electronics. Aerosol jetting, versus valve printing or inkjet printing, is well-suited for printing on 3D objects, offering a standoff distance up to 10 mm, a maximum part angular tilt of 30 degrees, and line widths as small as 15 microns.
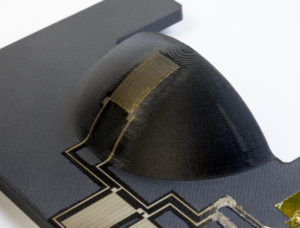
Strain gauge sensor on 3D-printed fiber-reinforced polymer. The sensor was printed with the IDS NanoJet Aerosol printer using a particle-free silver ink.
INKS
Inks well-suited for conformal electronic printing include nanoparticle conductive silver and gold inks, polymer insulating inks, and particle-free conductive silver inks. The ability to print or layer conducting and non-conducting features provides tremendous opportunity for the design engineer to create compact, lightweight devices. The conductivity of aerosol jet inks is significantly higher than the conductivity achieved with silver paste depositions.
MATERIALS
The material sets that inkjet and aerosol printing use are similar, though aerosol printing generally uses slightly lower viscosity inks (1 -10 mPa⋅s). Further, aerosol printing is better suited to print complex circuits or patterns on non-planar substrates.
Ink Types | Function | Applications |
---|---|---|
Silver, Gold | Conductor | Antennas, sensors, interconnectors |
Nanoparticle Conductive | Conductor | Antennas, sensors, interconnectors |
Polymer Insulating | Insulator | Multi-layer or surface normalizing |
Particle-free Conductive | Conductor | Polymer metallization, multi-layer circuits |
SUBSTRATES
Aerosol and valve direct-write technologies can conformally print complex 3D surfaces, as both methods have large standoffs and angular tolerances. IDS aerosol printing is exceptional, given its stable, multi-lens focused beams which enables high-resolution, defect-free deposition of electronic inks on various substrates. Typical substrates used in aerosol printing may include: glass, silicon, Liquid Crystal Polymer (LCP), Fiber- reinforced Nylon, Kevlar-Epoxy composites, Carbon Fiber Reinforced Polymer (CFRP), polycarbonate and polyimides.
Aerosol Jetting from IDS is uniquely designed to deliver satellite-free, overspray-free fine line printing over large stand-off distances and over a large range of angles. Reduction of satellites and overspray improves electrical performance of the components.
Substrate | Function | Applications |
---|---|---|
Liquid Crystal Polymer | Optoelectronics | Microelectronics |
Fiber-reinforced Nylon | Durable Structure | Automotive |
Kevlar-Epoxy Composites | Impact Resistance | Anti-ballistics |
Carbon Fiber Reinforced Polymer | Lightweight | Durable structures |
Polyimides | Flexible Substrate | Electronics |
DIRECT WRITE AEROSOL CAPABILITIES
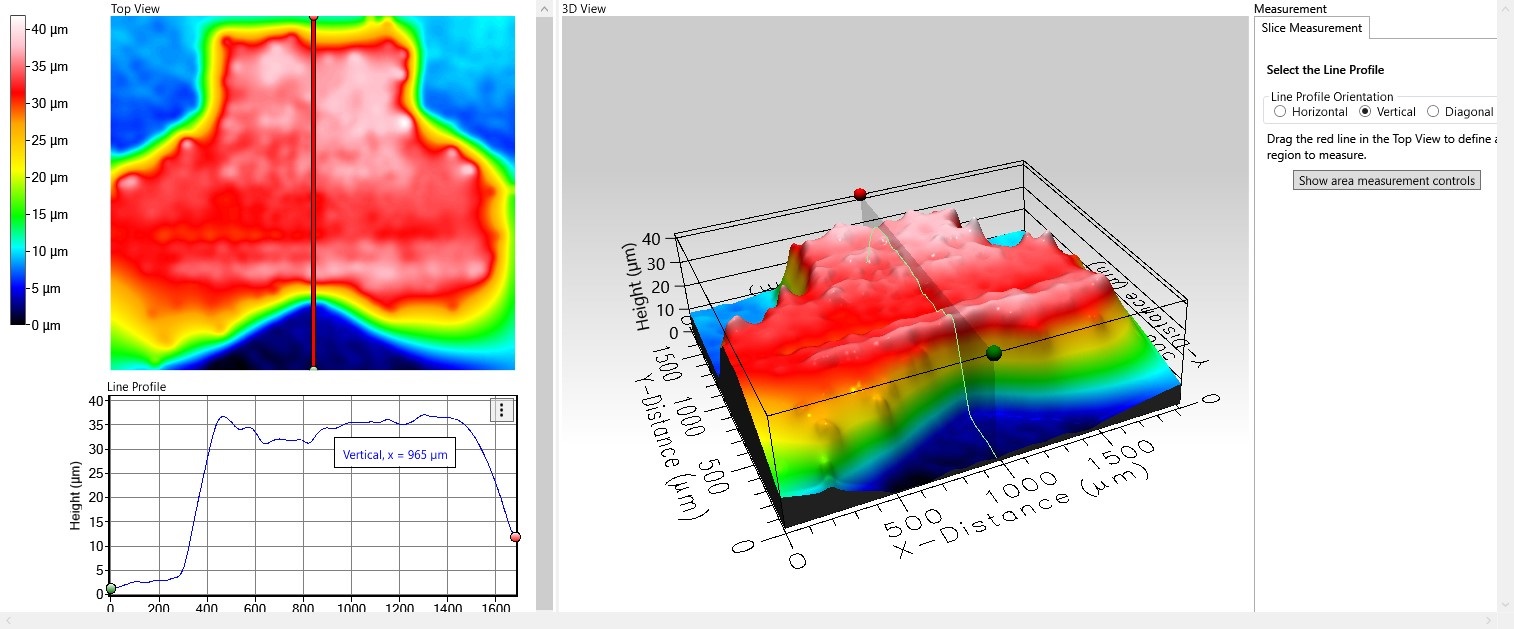
Aerosol direct-write printing distinguishes itself from inkjet printing or valve printing through the combination of superior edge definition, increased line height, minimum line width, and conformal printing capabilities.
Aerosol Jet has demonstrated defect-free printing of antenna structures with thicknesses greater than 35 microns on various polymer surfaces.
Satellite- Free Printing
Aerosol printing from IDS demonstrates superior satellite-free deposition, improving the electrical performance of the part.
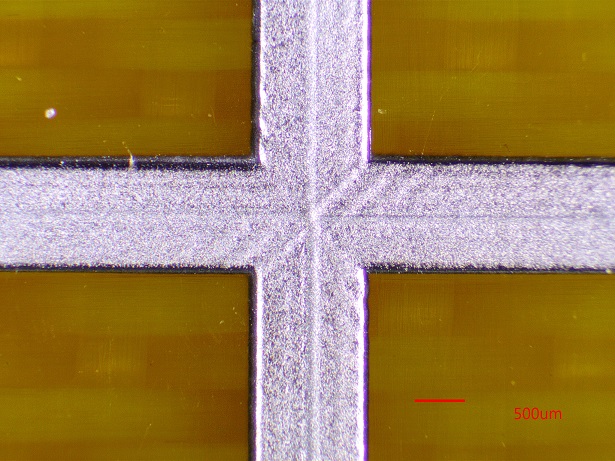
MINIMIZED OVERSPRAY
The unique aerodynamic lens assembly patented by IDS also minimizes overspray. Reduced overspray eliminates electrical breakdown between adjacent traces, and between traces and electronic components.
Non- Planar Printing
Aerosol-based printing enables non-planar or conformal deposition on curved or 3D surfaces. IDS aerosol printing leverages an annular sheath-aerosol flow to focus and collimate an aerosol distribution, as aerosolized droplets flow through two or more aerodynamic lenses. The IDS focusing and collimation method enables printing of lines with less than 10% dimensional variation, as the substrate height varies up to 6 mm.
The IDS high-accuracy printing improves consistency from part-to-part, without sacrificing quality.
Multi- materials/ Multi- layers
IDS aerosol printers can print layered conductive and non-conductive features serially, enabling printing of multi-layer circuits and vertical electronics. Furthermore, the ability to print non-conducting inks enables surface normalization of substrates with surface roughness of tens of microns. An initial surface normalization layer improves printed line thickness and height consistency, reducing the electrical resistance of conductive traces.
Production Stability
For production applications, operators and engineers need consistency over the course of a production shift or over several production periods. Consistency improves yields, increases useful production output, and simplifies designs. IDS aerosol printing can demonstrate less than 5% electrical and dimensional tolerance over the course of a typical 8-hour shift, day-after-day.
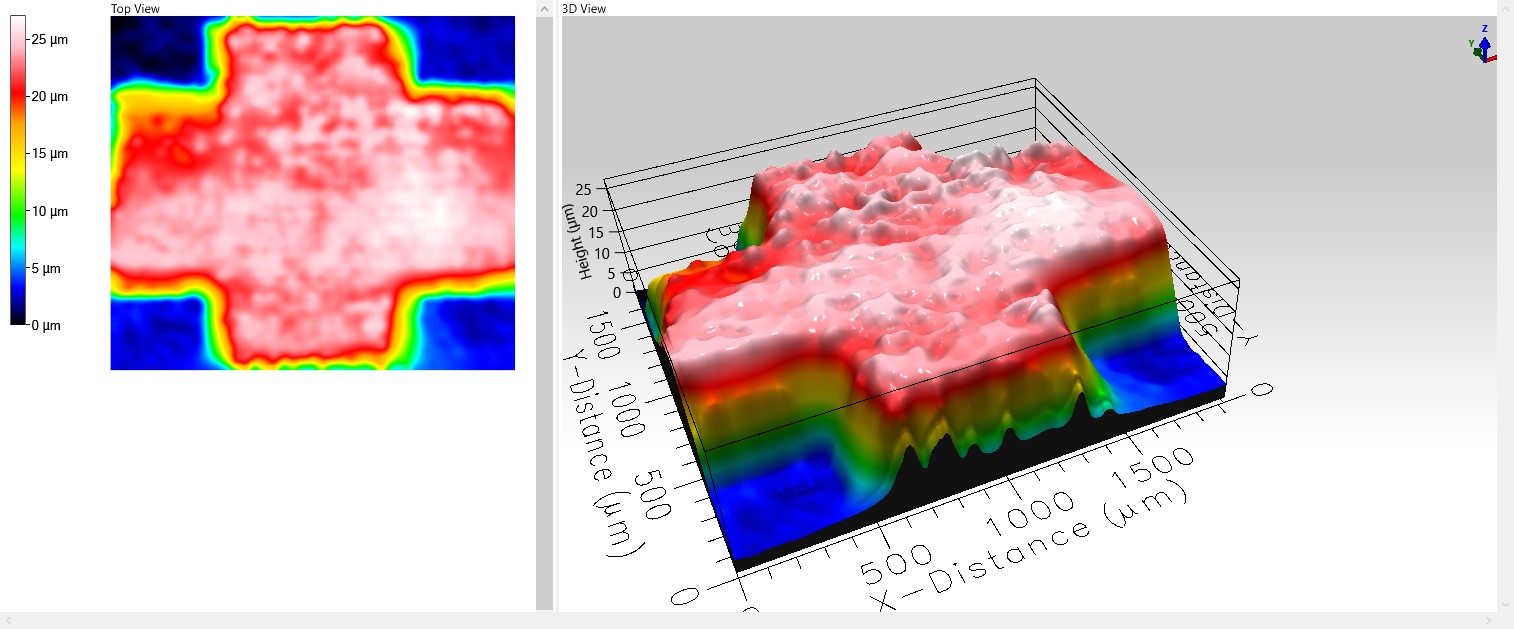
Capability | Aerosol | Ink Jet | Valve Printing |
---|---|---|---|
Satellite-free | ✓ | ✓ | |
Minimized Overspray | ✓ | ✓ | |
Non-planar | ✓ | ||
Multi-material / Multi-layer | ✓ | ✓ | ✓ |
Stability | ✓ | ✓ |