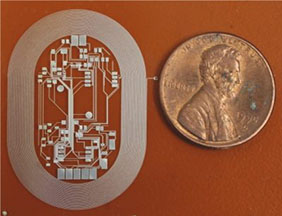
Interconnects and antenna features printed on Kapton®
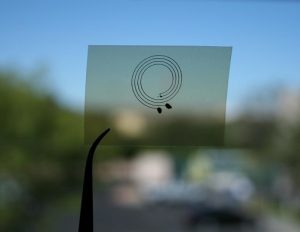
Flexible and transparent substrates
Direct Write Printing of Interconnects
Recently, there has been significant interest in direct-write printing of interconnects, especially for flexible electronics, circuit prototyping, and 3D “hybrid” printing. Aerosol printing, a form of direct-write printing (the other is inkjet) is uniquely suited to meet the needs of a variety of applications.
As engineers work to design a wide range of new and exciting devices, they may benefit from exploring aerosol printing: quick-turn prototyping of designs, conformal printing on non-planar surfaces, multi-material/multi-layer designs, and fine-line printing down to 15-micron widths, to name a few.
In choosing an aerosol technology over inkjet, one needs to consider the material sets (inks and substrates) as well as performance features of one technology over another.
Direct Write Capabilities
Capability | Aerosol | Ink Jet | Roll to Roll | Photo to Lithography |
---|---|---|---|---|
High-definition |
✓ |
✓ | ||
Fine-line |
✓ |
✓ | ✓ | |
Non-planar |
✓ |
✓ | ||
Multi-material/layer | ✓ | ✓ | ✓ | ✓ |
Stability | ✓ | ✓ | ✓ |
Aerosol Direct-Write Capabilities
Where aerosol direct-write printing distinguishes itself from inkjet printing is in the area of fine control. Inkjet printing is a good technology for directly-depositing a lot of material quickly. Aerosol printing generates finer features with greater precision than inkjet technologies.
High-Definition Printing
50 micron widths by 50 micron spacings are easily achieved with aerosol printing technologies. Some systems can achieve 15 micron widths with 30 micron spacings. Inkjet printing technologies typically deliver 200 – 1000 micron-wide lines, though there development systems capable of printing linewidths down to 50 microns.
Fine Line Printing
Aerosol printing, with its smaller droplet size is able to consistently deliver 15-30 micron widths and up to 5 micron heights per pass. These high aspect ratios are not possible in inkjet deposition schemes.
Non-Planar Printing
Non-planar or conformal printing is the deposition on curved or 3D surfaces, like a sphere. Aerosol printing leverages annualar aerosol-sheath flow to focus and collimate aerosol distribution as the droplets flow through one or more aerodynamic lenses. This focusing and collimation delivers the ability to print lines with less than 10% variation as the substrate height varies up to 6 mm. Printing of high frequency height changes may impart unique RF characteristics and will need to be properly designed for device performance.
Multi-materials/Multi-layers
Aerosol printers with dual-heads can either print gradients or layered conductive and non-conductive features. Accuracy is mostly limited by motion control systems of the provider or integrator.
Stability
For production applications, operators and engineers need consistency over the course of a production shift or over several production periods. Consistency improves yields, increases useful production output, and simplifies designs. Aerosol printing can demonstrate less than 5% electrical and dimensional tolerance variation over the course of a typical 8-hour shift, day-after-day.
Summary
Aerosol printing satisfies the unique needs of engineers looking to print on planar or non-planar surfaces, repeatably or in a low volume, high variation prototype environment. Aerosol printing can offer much finer lines with high aspect ratios which are needed for small and high-precision electronic applications. Finally, aerosol printing is flexible, whether or not your substrate is.